24" scale LPJRDC
Posted: Sun Oct 07, 2012 4:27 pm
I've been posting this build on a few other forums, but I figured since it's a shorty, you guys might want to see it, too. I'm actually making two at once, one is 24" scale with a rosewood board, and the other is 25.5" scale with a maple board. These are my first set necks, and my first angled headstocks. It's been a learning experience, for sure! I don't plan on making these guitars "pretty" necessarily, just trying to learn the building techniques as simply as I can. Here goes 

Didn't get around to making the body today. Went template crazy instead...
First I took my master template, which is (as far as I can assume) vintage correct, and I moved a few things around to make this work for me. Like I mentioned, I want this to have the bridge placed in a way that I can use the same fret slotting template to make either a 24", 25.5" or 28.625" scale guitar. So I made a copy of the template, but I didn't drill the bridge holes or cut the bridge pickup yet. After lining up a Tele neck to the end of this body, I was able to measure and determine where the 25.5" mark would be, with a Fender scale protruding down the neck. So I moved the whole template back to match that mark, and I drilled the bridge and routed the pickup based on a 25.5" scale length. It HARDLY looks any different; you'd have to compare it directly to the original to notice. I think it's a difference of about 1/2" or so...
The reason I want to make a set of templates to work this way, is not only to use the same fret scale template for all builds, but to have as little templates as possible, to create as many different guitars as possible. In this train of thought, I decided that if I made one fretboard template, I could make it long enough to do baritone fretboards, then anything shorter I could just cut it off at ashorter fret (see the various lines drawn near the end of the fretboard template) and then the heel of each neck would be identical, which would mean I could use one neck pocket template for all of these scale lengths. The only down side, if you think it's one, is that the shorter the neck is, the wider the nut will be. I made this template 1 5/8" wide at the nut of the baritone scale, and 2 3/16" at the heel. So a 25.5" scale would be as wide at the nut as the baritone is at the 2nd fret, and a 24" scale would be as wide at the nut as the baritone would be at the 3rd fret... What I didn't consider, until I was already burned out on making stuff today, is that this will then require 3 different headstock templates, to match the varying nut widths. But still, that's not as bad (to me) as having to make 3 fretboard templates and 3 neck pocket templates.
Here's what I have so far
Body template (made for 25.5" scale), fretboard template (made to work with all 3 scales), and a neck template made for each of the 3 scales (which will all intonate on this one body template). The flares on the headstock end are just to steer the router bearing away from the part of the blank that will become the headstock. I'll use a separate template for the headstock (check out my oh so clever headstock design )
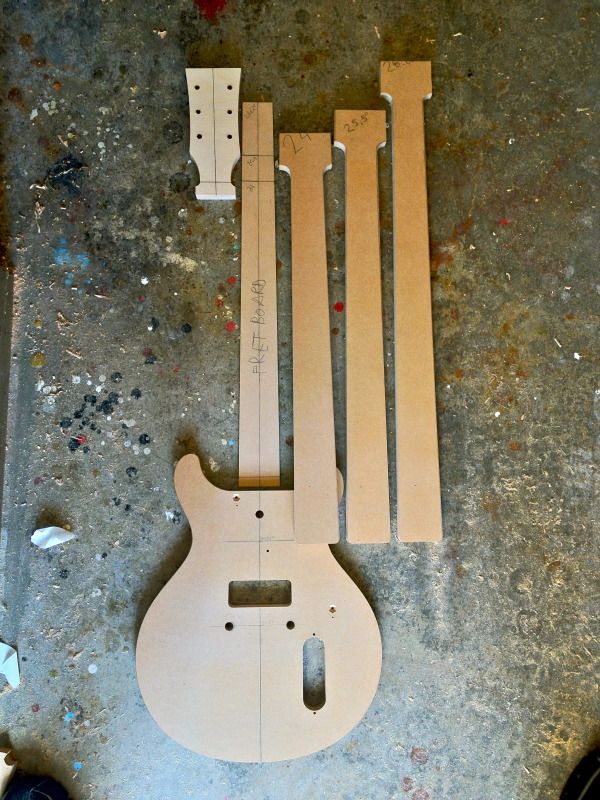
I double sided taped a, angled neck pocket template I'd gotten from Paul to a flat board, and I double sided taped my template to the top of that, then fed it through my planer until my template matched the angle of his. My tenon is wider than the one on Paul's template, so I made the mortise template from scratch by lining up one of my neck templates on it, then screwing pieces of straight-edged scrap around the neck to act as a guide for my router to cut a perfect pocket. It's very snug. It will be aligned and held in place by screws into the pickguard screw holes.
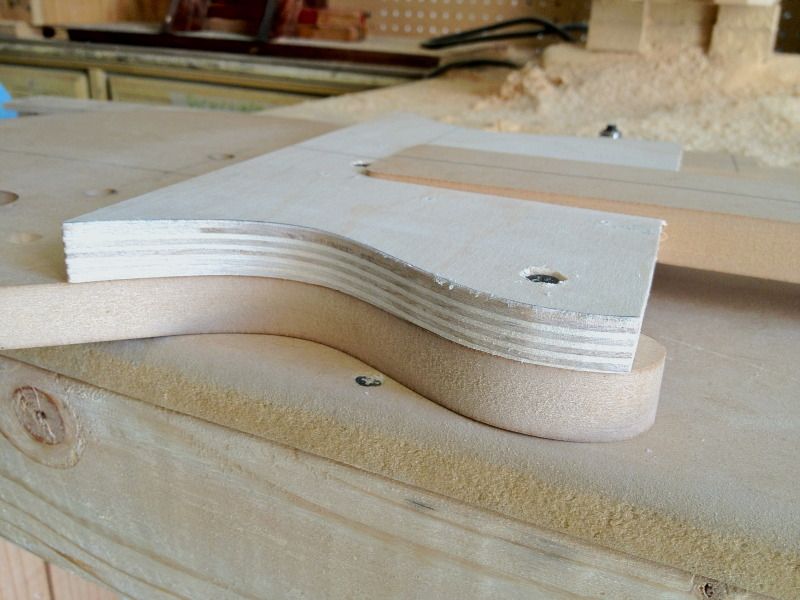
So that's where I am now. I need to make headstock templates to match the width's of these neck templates, and I need to make side profile templates. I will most likely have a volute on this, as I would hate to ever break the headstock...
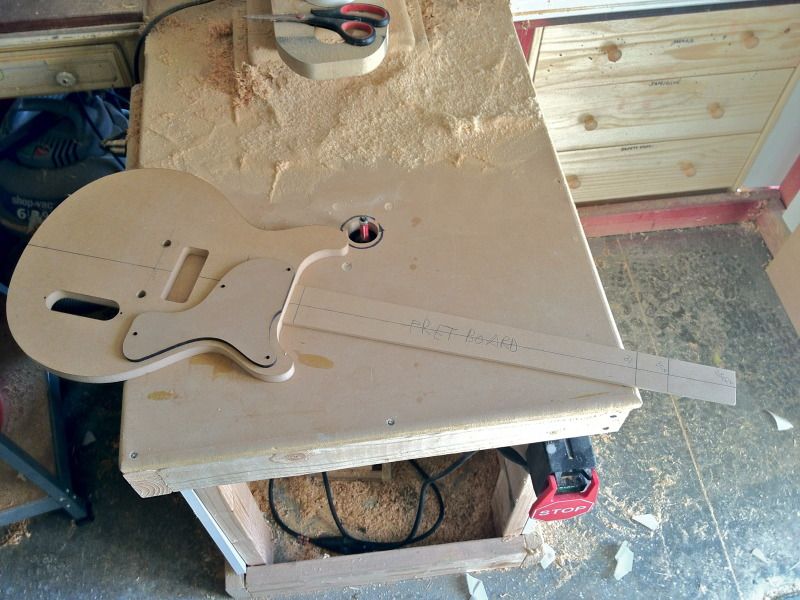


Didn't get around to making the body today. Went template crazy instead...
First I took my master template, which is (as far as I can assume) vintage correct, and I moved a few things around to make this work for me. Like I mentioned, I want this to have the bridge placed in a way that I can use the same fret slotting template to make either a 24", 25.5" or 28.625" scale guitar. So I made a copy of the template, but I didn't drill the bridge holes or cut the bridge pickup yet. After lining up a Tele neck to the end of this body, I was able to measure and determine where the 25.5" mark would be, with a Fender scale protruding down the neck. So I moved the whole template back to match that mark, and I drilled the bridge and routed the pickup based on a 25.5" scale length. It HARDLY looks any different; you'd have to compare it directly to the original to notice. I think it's a difference of about 1/2" or so...
The reason I want to make a set of templates to work this way, is not only to use the same fret scale template for all builds, but to have as little templates as possible, to create as many different guitars as possible. In this train of thought, I decided that if I made one fretboard template, I could make it long enough to do baritone fretboards, then anything shorter I could just cut it off at ashorter fret (see the various lines drawn near the end of the fretboard template) and then the heel of each neck would be identical, which would mean I could use one neck pocket template for all of these scale lengths. The only down side, if you think it's one, is that the shorter the neck is, the wider the nut will be. I made this template 1 5/8" wide at the nut of the baritone scale, and 2 3/16" at the heel. So a 25.5" scale would be as wide at the nut as the baritone is at the 2nd fret, and a 24" scale would be as wide at the nut as the baritone would be at the 3rd fret... What I didn't consider, until I was already burned out on making stuff today, is that this will then require 3 different headstock templates, to match the varying nut widths. But still, that's not as bad (to me) as having to make 3 fretboard templates and 3 neck pocket templates.
Here's what I have so far
Body template (made for 25.5" scale), fretboard template (made to work with all 3 scales), and a neck template made for each of the 3 scales (which will all intonate on this one body template). The flares on the headstock end are just to steer the router bearing away from the part of the blank that will become the headstock. I'll use a separate template for the headstock (check out my oh so clever headstock design )
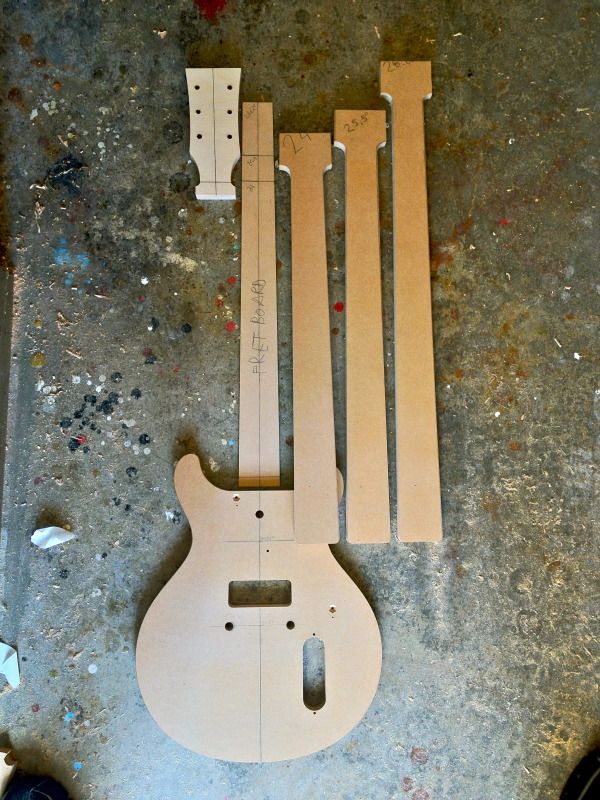
I double sided taped a, angled neck pocket template I'd gotten from Paul to a flat board, and I double sided taped my template to the top of that, then fed it through my planer until my template matched the angle of his. My tenon is wider than the one on Paul's template, so I made the mortise template from scratch by lining up one of my neck templates on it, then screwing pieces of straight-edged scrap around the neck to act as a guide for my router to cut a perfect pocket. It's very snug. It will be aligned and held in place by screws into the pickguard screw holes.
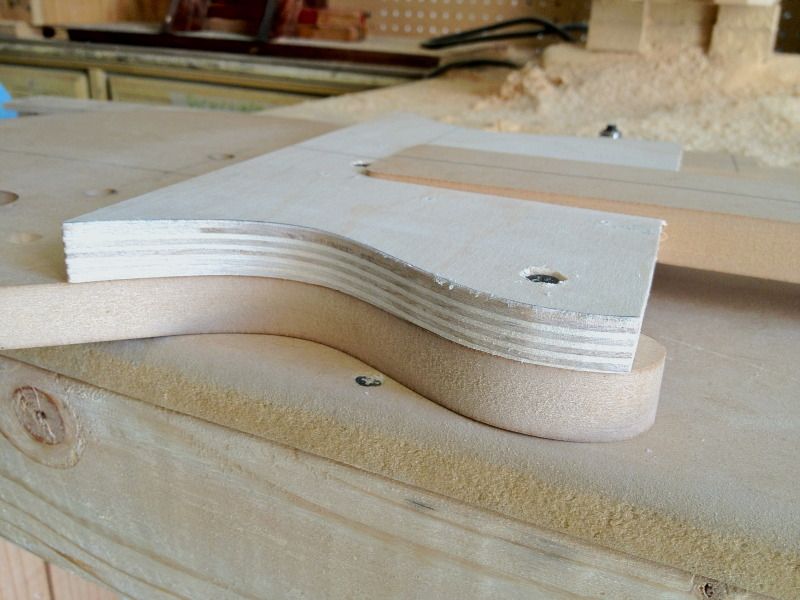
So that's where I am now. I need to make headstock templates to match the width's of these neck templates, and I need to make side profile templates. I will most likely have a volute on this, as I would hate to ever break the headstock...
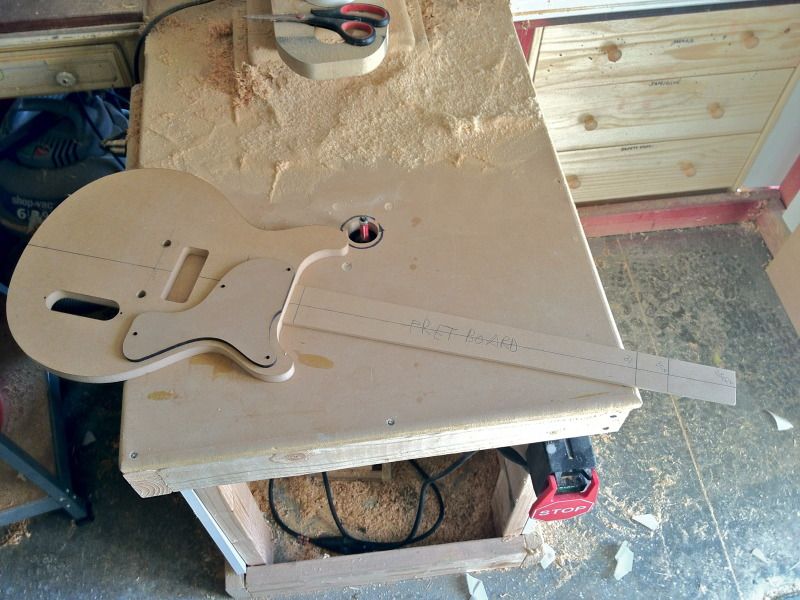